Calcium carbonate is an important and widely used inorganic salt mineral, commonly known as “industrial monosodium glutamate” and one of the commonly used fillers in various industries.
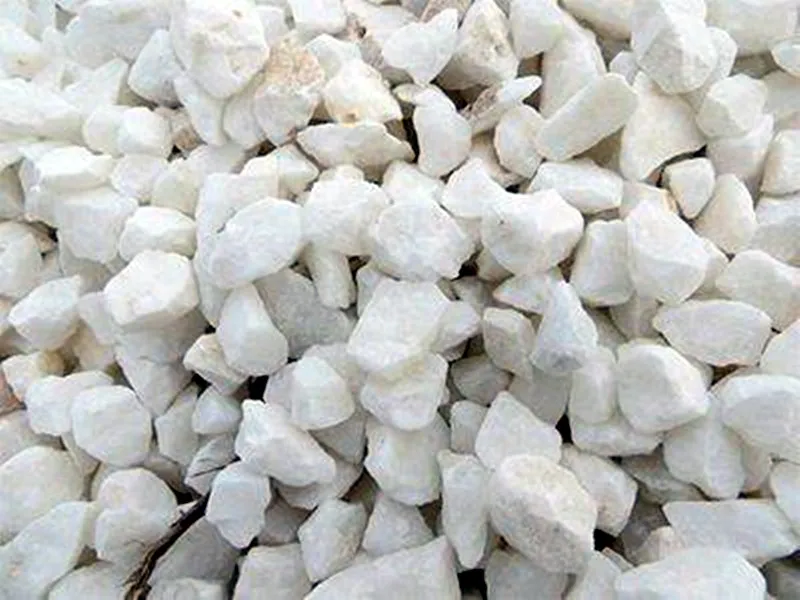
Main ingredients
Heavy calcium carbonate is mainly a powder material obtained by mechanical grinding and processing of natural minerals such as calcite, marble, limestone, chalk, and white marble as raw materials;
Light calcium carbonate is mainly a powder material obtained from limestone as raw material through processes such as calcination, digestion, carbonization, dehydration, drying, and classification.
Product bulk density
The difference in product bulk density is the most obvious difference between heavy calcium carbonate and light calcium carbonate.
The bulk density of heavy calcium carbonate products is relatively large, generally 0.8~1.3g/cm3;
The bulk density of light calcium carbonate products is small, generally 0.5-0.7g/cm3, and the bulk density of some nano-calcium carbonate products can even reach about 0.28g/cm3.
Oil absorption value
Heavy calcium carbonate has a low oil absorption value due to its large particles, smooth surface, and small specific surface area, generally around 40-60mL/100g;
Light calcium carbonate has fine particles, rough surface, and large specific surface area, so its oil absorption value is high, generally around 60-90mL/100g.
Whiteness
Heavy calcium carbonate has relatively more impurities, so the product whiteness is generally 89% to 93%, and very few products can reach 95%;
Light calcium carbonate products have high purity, so the whiteness is generally 92% to 95%, and some products can reach 96% to 97%.
Moisture content
The moisture content of heavy calcium carbonate products is generally 0.2% to 0.3%. The moisture content is relatively low and relatively stable. The moisture content of some high-end products can even reach about 0.1%;
Ordinary light calcium carbonate products have a moisture content of 0.3% to 0.8%, which sometimes fluctuates and is unstable.
Powder characteristics
The characteristics of heavy calcium carbonate powder are: irregular particle shape, and the particles have certain edges and corners, and the surface is rough; the particle size difference is large, the particle size distribution is wide, and the particle size is large. Crushing and refining will not change the crystal form of heavy calcium carbonate. Generally, calcite heavy calcium carbonate is in the hexagonal crystal form, and marble heavy calcium carbonate is in the cubic crystal form, which is mainly related to the place of origin.
The characteristics of light calcium carbonate powder are: the particles have regular shape and can be regarded as monodisperse powder; the particle size distribution is narrow. According to the shape of the crystal grains, light calcium carbonate can be divided into spindle-shaped, cubic, needle-shaped, chain-shaped, spherical, flaky and rhombus-shaped.
Particle size
Spindle-shaped calcium carbonate is the most common crystal form among light calcium carbonates, with an average long-axis particle size of 5-12 μm and an average short-axis particle size of 1-3 μm;
The average particle size of needle-shaped calcium carbonate is 0.01-0.1μm, and the average aspect ratio is 5-100;
The average particle size of chain calcium carbonate is 0.01-0.1μm, and the average aspect ratio is 10-50;
The average particle size of spherical calcium carbonate is 0.03-0.05μm;
The average particle size of cubic calcium carbonate is 0.02-0.1μm;
The average particle size of flake calcium carbonate is 1-3 μm.
Due to the incomplete reaction of calcium oxide, light calcium carbonate has a residual lime taste. It will have a choking taste when filling biscuits, while heavy calcium carbonate does not.
The particle size of heavy calcium carbonate products ranges from 0.5 to 45 μm. According to its original average particle size (d), it is divided into: coarsely ground calcium carbonate (>3μm), finely ground calcium carbonate (1-3μm), and ultrafine calcium carbonate. (0.5-1μm);
Application performance varies
Scope of application of calcium carbonate: plastic products, rubber, papermaking, EVA foaming, shoe materials, artificial leather, coatings, inks, building materials, wires and cables, handicrafts, adhesives, toothpaste and other industries.
During the application process, heavy calcium products are mainly used in industries such as papermaking, rubber and plastics. The filling amount is generally large and they are mainly used as volume fillers to reduce the manufacturing cost of applied products. Light calcium products have a relatively wide range of applications, mainly for volume filling, while nano calcium carbonate products are often used as functional fillers such as modification or reinforcement during the application process, and the filling amount is generally small. The main application areas of light calcium carbonate products are plastics, rubber, coatings, adhesives and inks.
Taking plastics as an example, calcium carbonate is widely used in filling resins such as polyvinyl chloride (PVC), polyethylene (PE), polypropylene (PP), and acrylonitrile butadiene-styrene copolymer (ABS). Adding calcium carbonate has a certain effect on improving certain properties of plastic products to expand their application range. In plastic processing, they can reduce resin shrinkage, improve rheology, and control viscosity. It can also play the following roles:
(1) Improve the dimensional stability of plastic products
The addition of calcium carbonate plays a skeleton role in plastic products and plays a great role in stabilizing the size of plastic products.
(2) Improve the hardness and rigidity of plastic products
In plastics, especially soft polyvinyl chloride, the hardness gradually increases with the amount of calcium carbonate added, and the elongation decreases with the increase in hardness. Calcium carbonate with fine particles and large oil absorption value has a large hardness growth rate. On the contrary, calcium carbonate particles with a small crude oil absorption value will have a small hardness growth rate of the plastic. Among soft polyvinyl chloride, heavy calcium carbonate has the smallest hardness growth rate, followed by precipitated calcium carbonate (light).
Calcium carbonate generally cannot play a reinforcing role in plastics (resins). Calcium carbonate particles can often be infiltrated by resin. Therefore, the normal function of adding calcium carbonate is to increase the rigidity of the resin and increase the elastic modulus and hardness. As the addition amount increases, the tensile strength and extreme elongation decrease.
Different calcium carbonates, with different amounts added, will have different hardnesses.
(3) Improve plastic processing performance
The addition of calcium carbonate can change the rheological properties of plastics. Calcium carbonate powder is often added in large quantities, which helps it mix with other components and also helps in the processing and forming of plastics.
The addition of calcium carbonate, especially the addition of surface-treated calcium carbonate, can not only improve the hardness of the product, but also improve the surface gloss and surface smoothness of the product.
The addition of calcium carbonate can reduce the shrinkage, linear expansion coefficient, and creep properties of plastic products, creating conditions for processing and forming.
(4) Improve the heat resistance of plastic products
Adding calcium carbonate to general plastic products can improve the heat resistance. For example: adding about 40% calcium carbonate to polypropylene can improve the heat resistance by about 200C. When the filling ratio is ≤20%, the heat-resistant temperature increases by 8 to 130C.
(5) Improve the astigmatism of plastics
Among plastic products, some products require whitening and opaqueness, while others want to be matted. The addition of calcium carbonate can play a certain role in this regard.
Calcium carbonate with a whiteness above 90 has an obvious whitening effect in plastic products. Combined with titanium dioxide and lithopone, the matt properties of plastic products are greatly improved.
In calcium plastic paper, in low-density polyethylene (LDPE) and high-density polyethylene (HDPE) films, adding calcium carbonate can achieve the effects of astigmatism and matting, making it suitable for writing and printing.
Calcium carbonate with better whiteness can also replace expensive white pigments.
(6) Products can have certain special properties
Calcium carbonate added to cable materials has a certain insulating effect. The addition of calcium carbonate can improve the electroplating performance and printing performance of certain products.
Fine or ultrafine calcium carbonate is added to polyvinyl chloride (PVC) to have a certain flame retardant effect.
(7) Reduce the cost of plastic products
The prices of ordinary light calcium carbonate and heavy calcium carbonate are far lower than the price of plastic. The addition of calcium carbonate will reduce the cost of plastic products. Calcium carbonate is called filler or extender abroad.
At this stage, the main goal of adding calcium carbonate is to reduce the cost of plastics. With the improvement of the surface properties of calcium carbonate and the controllable shape and particle size, calcium carbonate will gradually become a functional filler for the purpose of reinforcing or imparting functionality.